Mixed plastic waste is converted into Liquid RDF through In-Vessel Depolymerisation. Oil, Residual Carbon and Gas is generated by processing.
METHODOLOGY OF THE PROCESS
- The process is termed Random Depolymerisation. It is the degradation of bonds to breakdown of polymers into monomers randomly
- The process is carried out in a special designed vessel in absence of oxygen & in the presence of certain catalytic addictives
- This process is utilized for the degradation of plastic to lower hydrocarbons
- There are no affluents in the process, the water used in this process is recyclable.
- The oil is fed into the engine to generate power for sale.
- The gas generated in the process is rich in Propane, Butane, Mathane, Carbom monoxide and Hydrogen is reused in the process for heating the depolymerisation vessel
- The residual carbon is used for landfills or sent to cement plants
- Initially the plant runs on LPG and diesel to start up
- Once the process is underway and the gas in generated within the process, external source of energy is disconnected and the plant is self sufficient
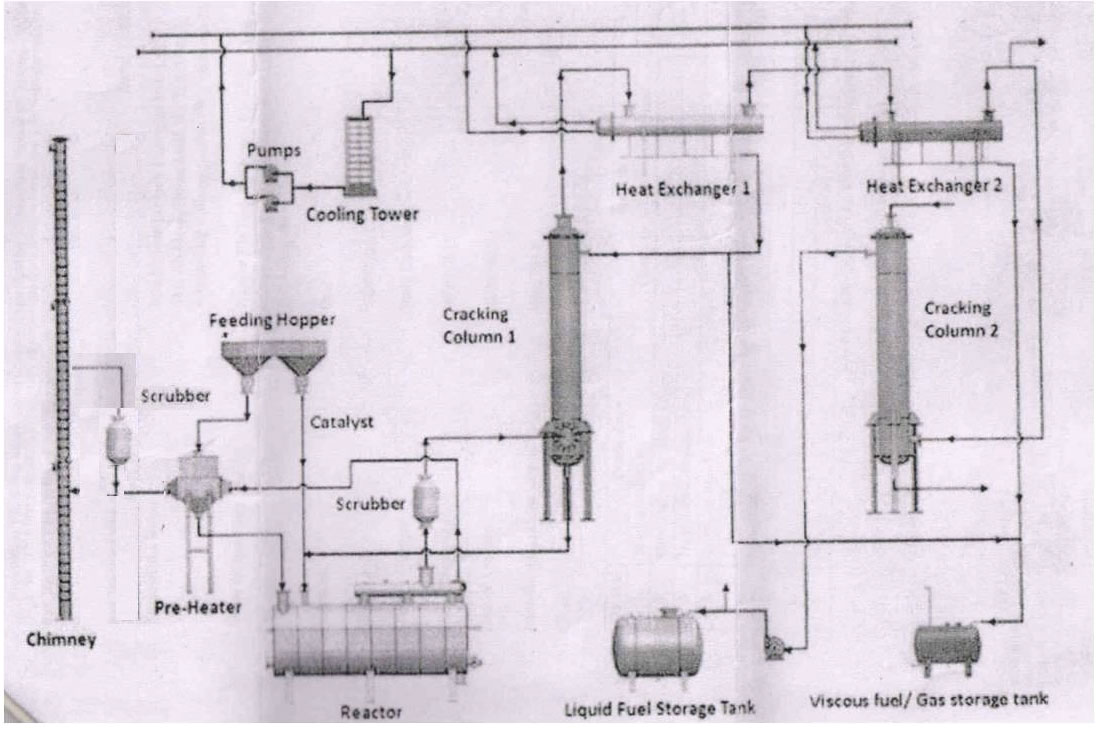
Line Diagram of the Plant
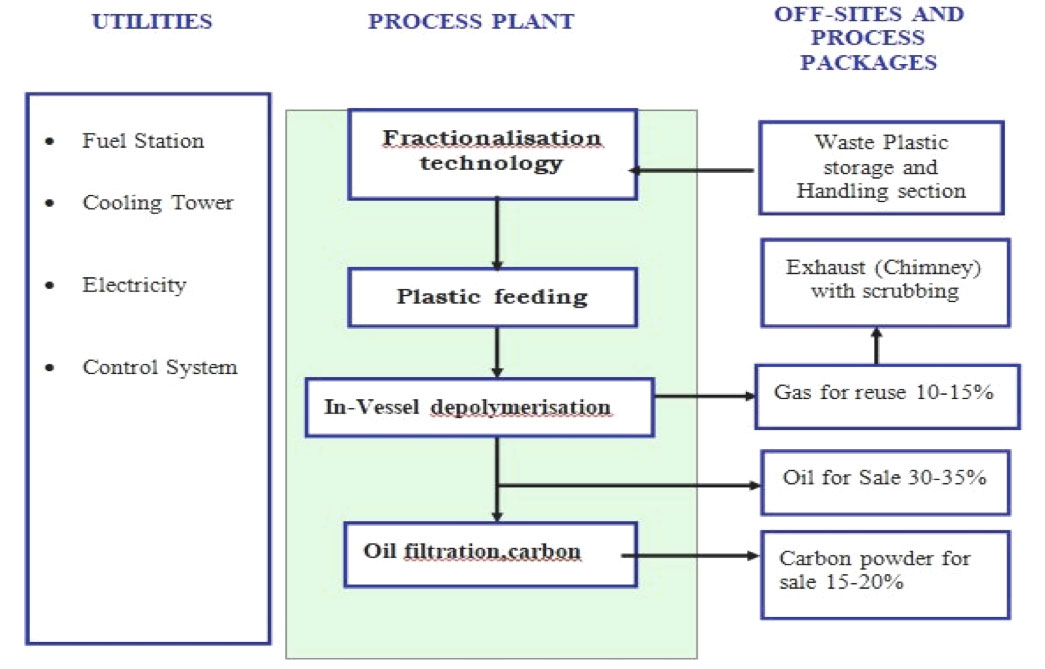
Process lock Diagram of Depolymerisation
Highlights of the technology
- Modular Design 5, 10 and 20 TPD capacities
- Capable of Handling Mixed Plastic including Multi Layered Plastic
- Established end of Waste Process confirming to Global Environmental Emission Standards
TECHNICAL SPECIFICATIONS: LIQUID RDF
Furnace Oil (FO) | Liquid RDF | |
---|---|---|
Density(g/cc) | 0.89 - 0.99 | 0.8 - 0.98 |
Flash Point(degree C) | 66 | 70 - 85 |
Pour point (degree C) | 20 | NA |
CGV (kcal/kg) | 10,000 | 9895 |
Sediment, % Wt. Max. | 0.25 | 0.25 |
Sulphur, % Wt. Max. | 2 -4.0 | 1.5 - 2.5% |
Water Content, % Vol. Max. | 1% | 1% |
Ash, % Wt. Max. | 0.10% | 0.1 - 0.15% |